3D Patterns in wood working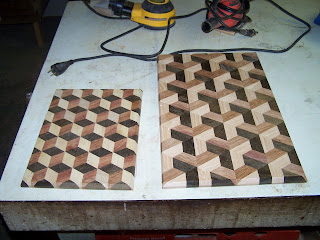
Hey there fans.
For some time I have been experimenting with designs in wood art. Some of them make it to my grandfathers lathe and some are used in a flat design, (cutting boards, lazy susan’s etc.) The 3D concept is a fun project and although it has particular challenges, they can be overcome with practice and determination (not to mention a lot of wrongly cut pieces in the scrap bin).
So without any further ado, lets get started.
Lets start with the tumbling block design.
As you can see this design is made up of diamonds. These diamonds take some time and lots of scrap to get just right. You will need a very accurate mitre box or cutting tool to get these just so. Proceed only after you have a very tight uniform result or you will be chasing gaps and spacing in the glue up and never get a good result. Start with pine before you get into the expensive stuff. Here you see I have chosen ash, brazilian walnut and brazilian cherry. Go for an equal contrast, ie: pick types of wood of equal denisity and hardness and more important for the 3D, equal distances of diversity in color. Two colors that are similar will highlight the third and diminish the depth of the 3D’ish,ness ??? (is that a word) of the work.
Back to the cutting, each piece must be uniform in length and length of cut. What does that mean? Well, they need to be equal length across the cut and the running grain. All 4 sides must be equal for this to work. The width of your material will form 2 sides. Likewise the length of your saw cuts will form the other 2 and must be equal to the first two. This takes some practice and a couple of custom jigs to get just right. The coolness in the character of the 3D design is enhanced by the smaller diamonds but the smaller are much more difficult to get right. A smaller diamond tumbling block design is a real eye catcher every time but start with the larger on your first try for simplicity sake.
I start the gluing with 3 diamonds and a hexagon. If I use any clamping (which I usaly do not) it may be a rubber band. Holding them in place for 10 seconds is more than enough though without any assistance or clamps, then just set them aside to dry. If your cuts are right you need not force a better fit with clamps.
In all wood working you can not and should not make up for bad jointery with clamps. This will internalize stress within the piece which will some day find its way to the surface and express itself. Besides, wood has enough issues all on its own (moisture content, grain stress etc.) without us adding to the mix.
Here we are combining the hexagons into groups of 3. When you do it this way it is essential that you clean all the glue off the exposed or unused (exterior) sides or this glue will keep your next glue up from going well. I use my wife’s tooth brush, please don’t tell her.
Coming along fine
The problem with these 3D designs is always jointery and glue up. You are essentially gluing up hundred of joints simultantously verses multigenerational work in which the sections of multiple pieces are joined, a much easier thing to do. Jigs help but honestly it is a mess. Don’t spare on the glue, get it everywhere. Here is my glue up jig being used to hold for the belt sander. I do run these through the planer also but only for uniformity and only a 32nd or 64th off in any one pass.
Here is a hint on glue up jigs you will love. There is a material that is used to paint the ends of lumber to keep it from drying too quickly and also used to cover exotic woods so their moisture content does not change. You know the stuff right, essentially a liqud wax which hardens into a coating. This stuff is not hard to get and is sold by the gallon. I coat all my jigs with it, especalay my glue up jigs. I use it on my some of my tools also. Brush it on and wait 24 hours and nothing will stick to your jigs. It is God’s gift to those of us who love glue.
ere is a close up of this piece which is a cutting board.
And here is the final product with edges of a 45 degree. With this design rounded edges do not seem to compliment the work. Now we finish sand up to 400 grit and apply finishing oils that are food friendly